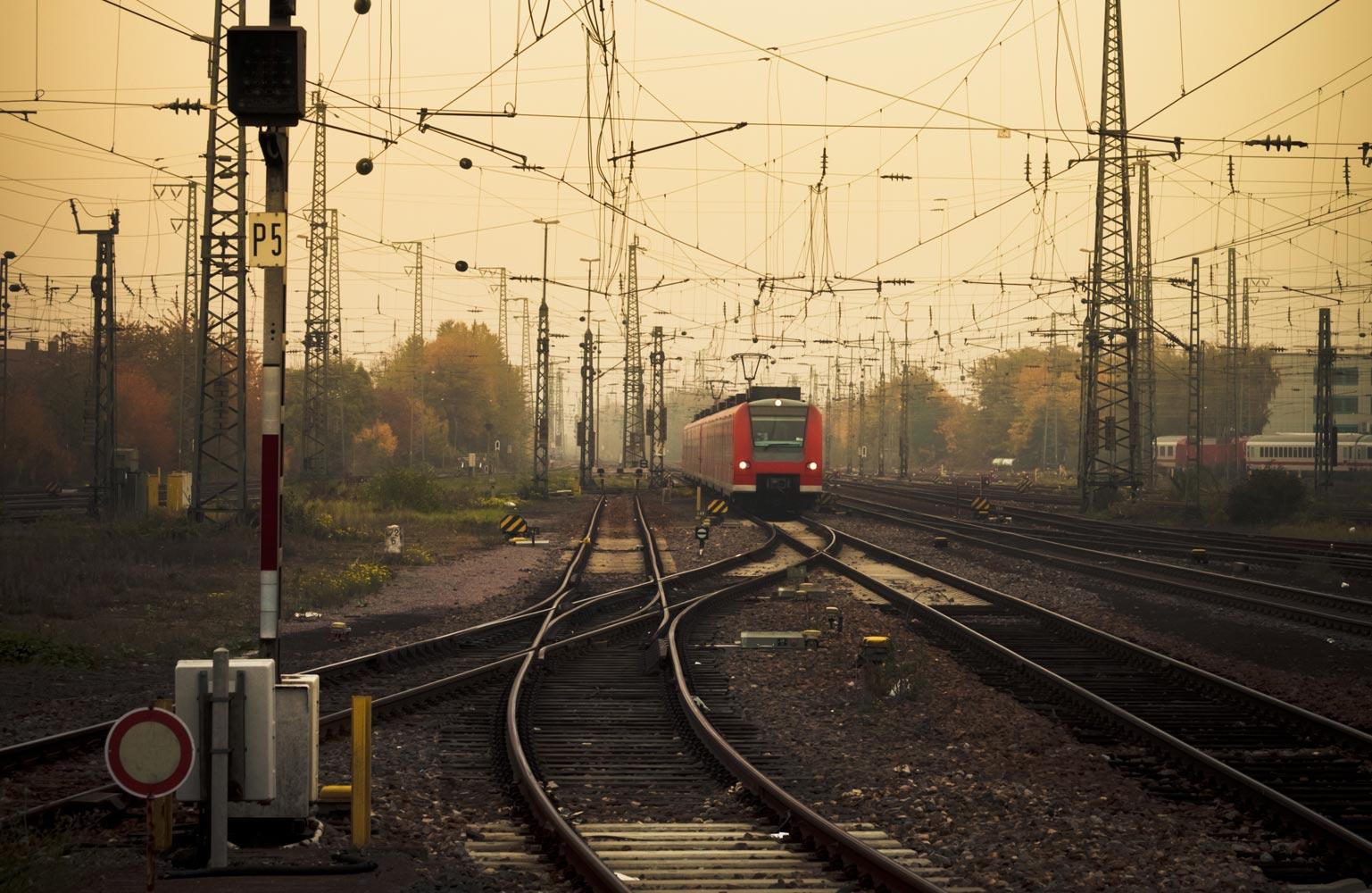
Mechanical Locomotive and Railcar
IT Newsletter Jan - Feb, 2016
January/February News
Line of Road Failures - Phase I
With this project, cars are being identified that cause multiple undesired emergency events. Previously, the only information we had was that 1 of the many cars on the train was probably responsible for the UDE, but no way to figure out with certainty which one it was. So these cars went on, often for months, intermittently causing train delays over and over again. Each event costs UP about $1,000 in train delay and recrews. By combining the data with the other railroads, we can track these cars better by finding common cars in multiple failed trains - allowing them to "bubble up" the bad actor list until they stand out from other cars. Per Bill Sheesley, we think we're after only about 1,000 cars, but if every one causes just 3 events, we're up to $3M in costs to UP! Since we're sharing this data with Railinc, our contribution not only helps UP, but also helps fluidity on all the Class I's.
A joint team from Mechanical, Safety, Operating Systems, and IT have been scrubbing the data for the last several months. One last verification took place in the first half of February, with a plan to start sharing this data with Railinc the week of February 15th, 2016. The second phase is targeted for 3rd quarter, 2016. Mike Pfeifer's team will be responsible for receiving the shared UDE information from Railinc and using the data to systematically determine the bad actors.
Capturing Component IDs - Brake Valves
The Component Tracking program (formerly known as CEPM) is a multi-phase, multi-year initiative to create an industry process and related technology tools for capturing data related to railcar equipment components.
Brake Valves
On Feb 9th, IT enabled the ability to capture the component ids for the emergency and service portion of the brake valve. See screenshots below, indicating the various UP IT systems where brake valve info can be captured.
Benefits: The data produced by this effort gives UP the capability to do analysis that will lead to longer component life and purchase price reductions. UP purchases about $7M in brake valves and has around $14M in brake-related failures in a 12 month span. Assuming we can get a 2% reduction in the failure category, there is potential for $280k/year in savings.
In general, capturing unique component ids provides a common indentifier across all roads and manufacturers. This info also provides visibility into rail equipment health and performance, enabling managers to make decisions that improve rail safety, reduce costs associated with equipment maintenance, and run more efficient and effective rail operations.
UP Systems supporting brake valve component ids....
CEPM
Car Task Closeout (CTC) in MCS
Car Repair Billing (CRB)
Automatic Bad Ordering of Cars with High Risk Wheels
Failure Analysis Reporting
"Cool" Labels
We LIKE the picture below of Greg Thompson, standing by some well-organized material bins! The labels on the bins were just a small piece of the overall Material Tracking and Planning (MTP) project, currently being supported on the Mechanical side by Mike Kadar and Jim Brix. Always good to see what was developed is being used and provides value to the field!
Employee Training Exercise Updates
To keep the various training systems terminlogy in synch, a recent request was made to use the terms "On Standard", "Coaching", "At Risk" vs. "Pass", Fail", "Hearing" in relation to the employee's test results. The ETE changes were introduced on 2/8/15. The below gallery shows a sample of the changes introduced to the ETE system.
Implementations
MCS - 2/9/16
This implementation was not minimal, based on sheer numbers. We implemented 288 windows in support of an upgrade to GEN 8.5. This was necessary in order to be on a supported version of the GEN tool, upon which MCS is based. In addition, updates to the Denver and Houston/Englewood SFM maps were provided, as requested.
ILP2 - 2/9/16
One of the major benefits of this implementation was a revamping of the Supervisor Planner to improve usabilility. New sorting capablities, links, visual aids were added.
MTP - 2/11/16
Various customers requests were fulfilled in this implementatios. Seventeen requests were closed related to Material Ordering, Item Search, Request History, Manage Inventory, PPS, and Warranty.
Upcoming Events
MCS Monthly Implementation
Tuesday, Mar 1, 2016, 10:30 AM
undefined
ILP2 Cutovers
- February 2nd - South Morrill
- February 16th - Livonia
- March 14th - Commerce/Delores
- May 2nd - Houston
Questions?
Email: rrdonaho@up.com
Phone: 402-544-0832